環境改善と脱炭素
05.環境改善と脱炭素
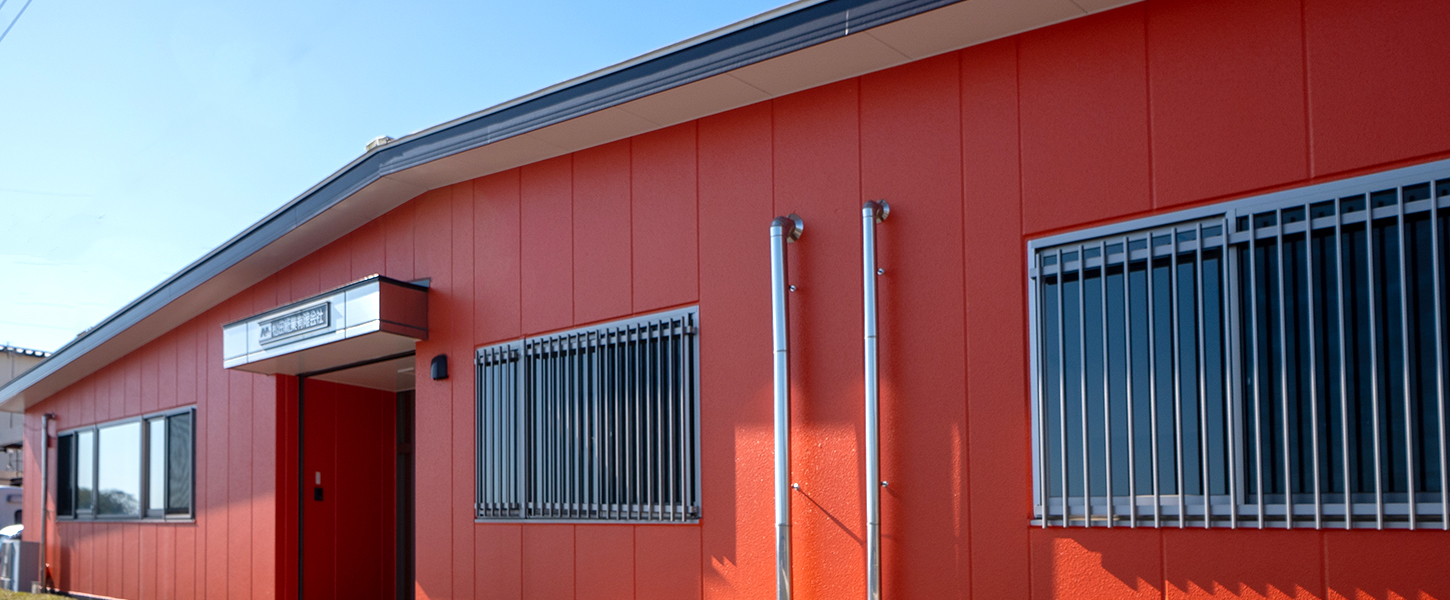
働く環境の改善が地球環境保護に
年間使用電力量推移
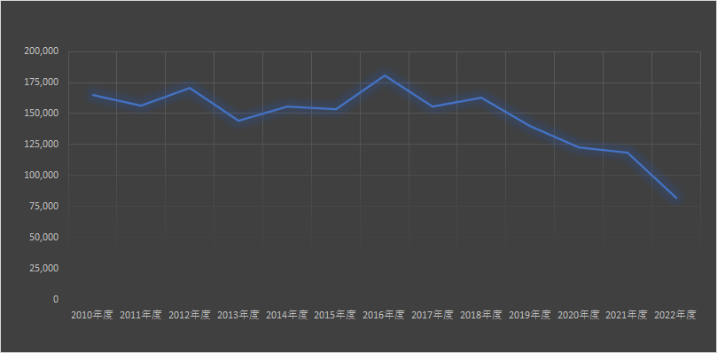
2008年の工場移転以来、大きな音や紙粉にまみれる工場内の労働環境の改善に努めてまりました。
気がつけば、取り組みにより使用電力量が計測開始当時の2010年と比較して50%の削減につながっていました。
社員の健康を考えた工場内の環境づくりは、地球環境保護に貢献する結果となっていたのです。
2023年には、太陽光発電システムを採用。
これからもさらなる労働環境の改善を目指すとともに、地球への恩返しをしていく所存です。
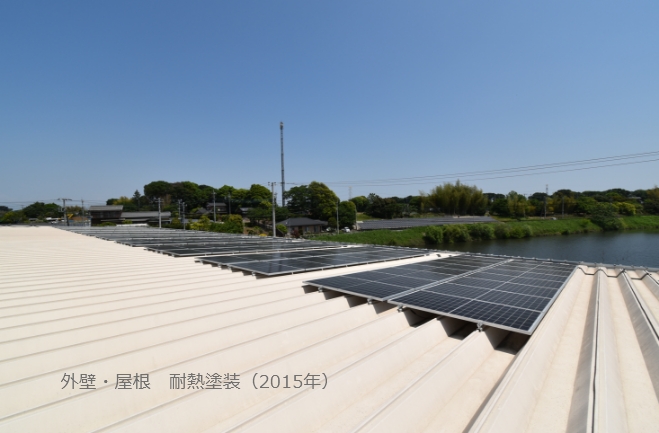
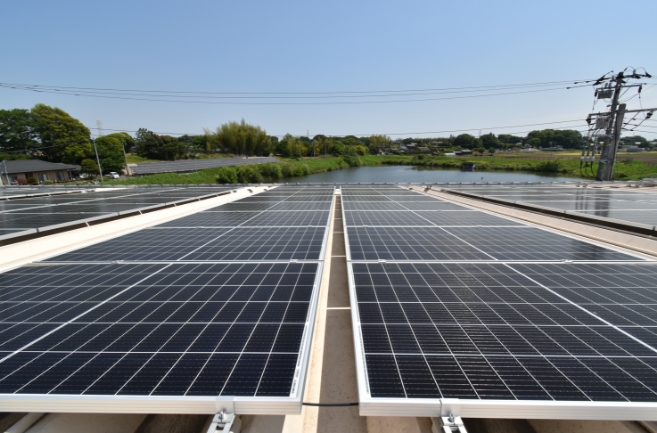
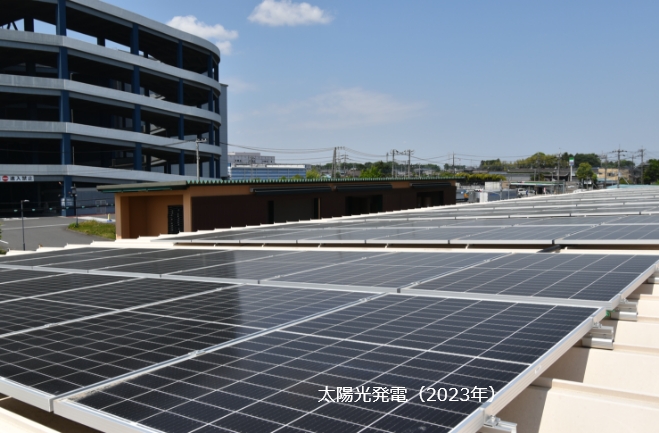
[脱炭素につながる松田紙業の取り組み]
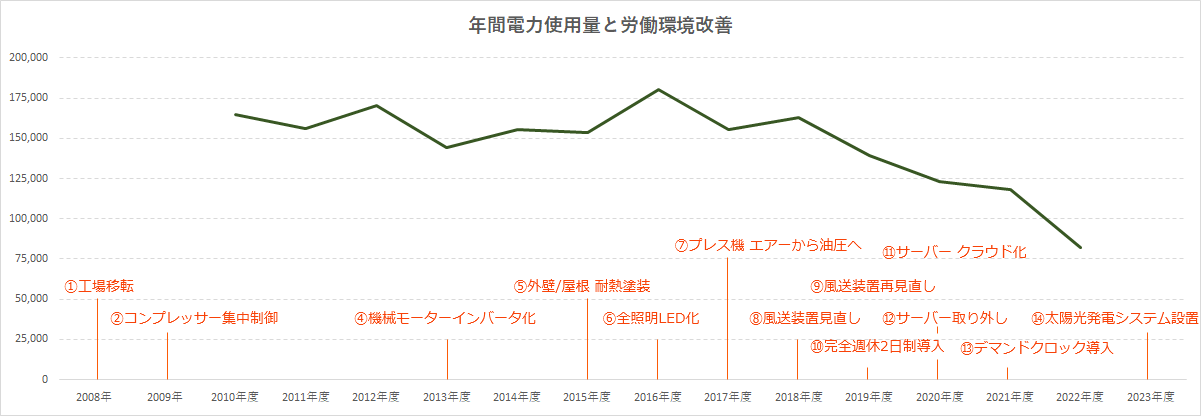
①工場移転 /抜本的環境改善 2008年度
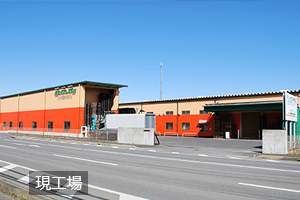
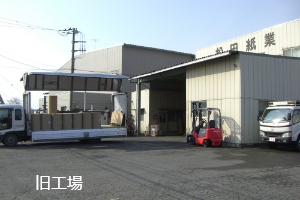
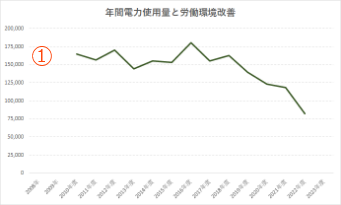
空調が不十分なため現場の社員にとって過酷な職場環境、虫などの異物混入による危惧の問題、工場が外から丸見えのため取引上のセキュリティーの要請に応えきれない問題から工場を移転。
②コンプレッサー集中制御 /音・風・熱の削減 2009年度
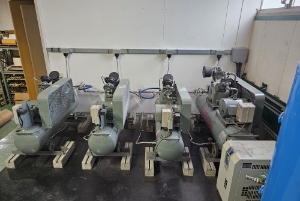
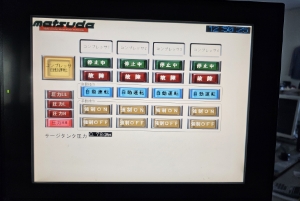
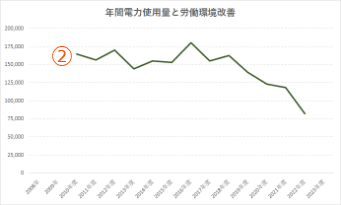
もともとスリット機械1台にコンプレッサーを1台使用していた工場内。
すべての機械に対し稼働するコンプレッサーを最小1台で済むよう集中管理。
これにより、稼働が効率的に。
同時にコンプレッサーの作業員に対する「音」「風」「熱」の負荷問題が劇的に改善。
③機械モーターインバータ化 /音・風・熱の削減 2013年度
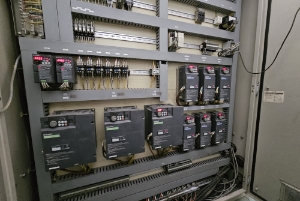
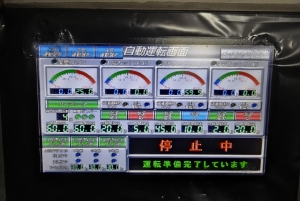
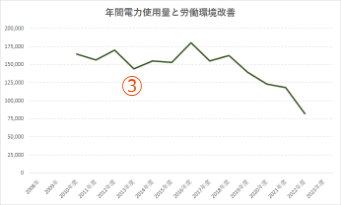
スリット機械のモーターをインバーター化。
依頼に合わせてモーターの回転速度や加速度を柔軟に変えることができるように。
これによりさらに「音」「風」「熱」の環境を改善。使用電力量も目に見えて減少。
④外壁・屋根 耐熱塗装 /熱の削減 2015年度
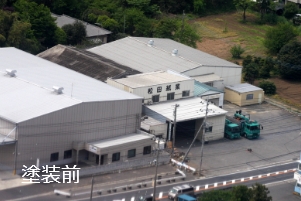
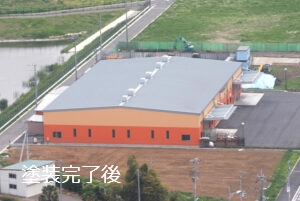
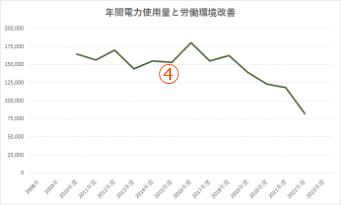
屋根と壁に遮熱塗料を採用。
反射熱がなくなり、工場内の暑さが軽減。
⑤全照明LED化 /虫混入の予防・人体にやさしい環境へ 2016年度
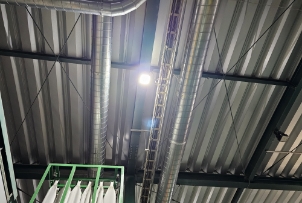
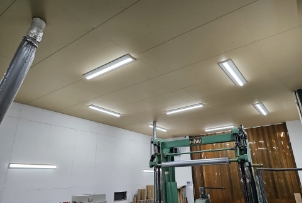
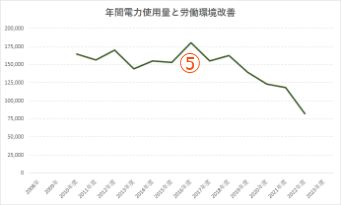
全照明をLED化することにより、紫外線や熱線の放射量が少なくなったことで発熱が減り、虫が入りずらく、作業員の目や皮膚にやさしい環境へ
⑥プレス機 エアーから油圧へ /風の削減 2017年度
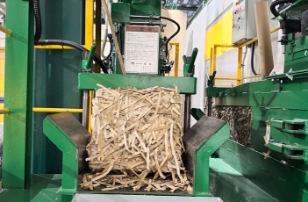
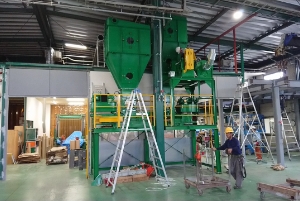
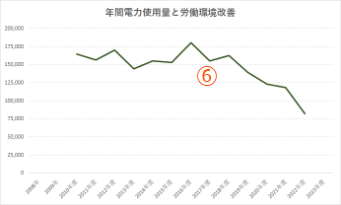
エアーシリンダー式のプレス機から油圧シリンダー式のプレス機を導入し、「風」の出ないプレス機へ
⑦風送装置見直し /空気の正常化 2018年度
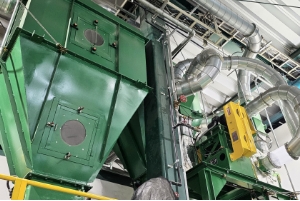
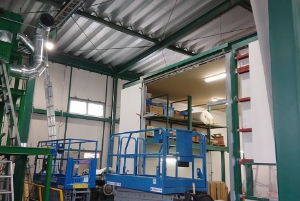
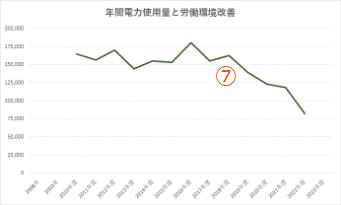
配管・空気の流れを見直し。
これにより過剰に送っていた空気を適切で十分な送風にすることが可能に。
⑧完全週休2日制導入・風送装置再見直し /労働環境向上 2019年度
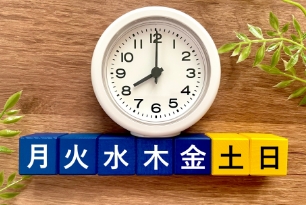
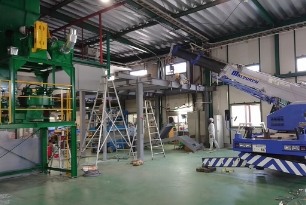
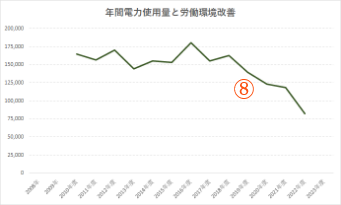
完全週休二日制を導入し、社員にゆとりを。
風送装置を再度見直したところ、使用電力が一気に下がる。
⑨サーバー クラウド化・サーバー取り外し /音・熱の削減 2020年度
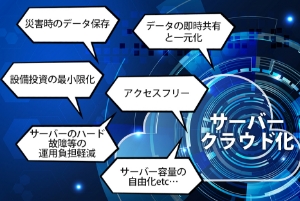
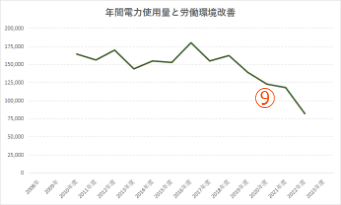
サーバーのクラウド化、そして取り外し。サーバールームのエアコンOFFへ。
「音」「熱」の低減へ。
⑩デマンドクロック導入 /電力の見える化 2021年度
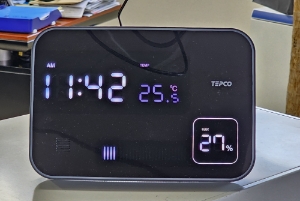
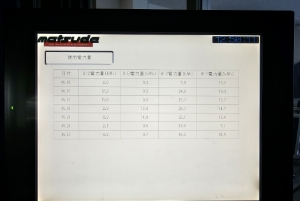
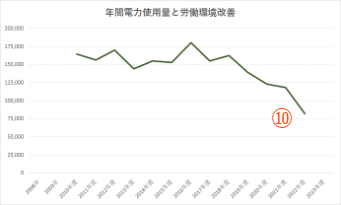
デマンド(平均使用電力)の見える化 + 警報装置設置
使用電力が目視で確認できるため、社員全員でCO2削減への取り組みへ。
⑪太陽光発電システム導入 /自然エネルギー使用によるCO2削減へ 2022年度
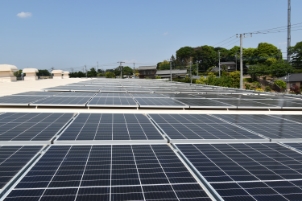
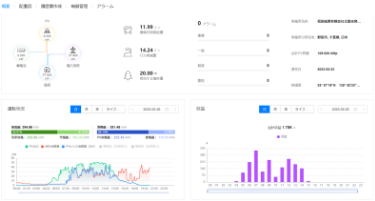
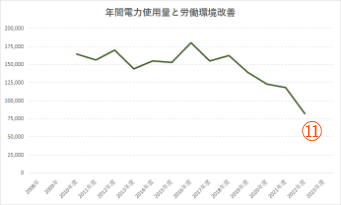
工場の屋根に太陽光パネルを設置。発電量、消費電力量など、リアルタイムに確認可能。
生まれた電力は工場稼働で使用。
2008年度の工場移転後、労働環境の改善をひとつひとつ図ってきました。
結果、節電そして脱炭素へとつながっています。
これからもわたしたちの理念をもとに
人が心地よく働くことができる環境づくりに挑戦してまいります。